CF Cartridge Filters
Effective Fine Particle Control Using New Filtration Technology
CF Cartridge Filters
-
Solutions
-
Legal
-
Health
-
Efficiency
The airborne dust is drawn into the filter by a fan along a distribution chamber. This chamber ensures an even flow of air through the filter cartridges and decelerates the air stream. This reduction of speed coupled with the physical change of direction, ensures that the large particles are separated from the air stream. The air stream containing the remaining dust is drawn equally onto the outer surface of the cartridge pleated polyester filtration elements. The dust is retained on the surface and the air permeates through the filter media to the inside of the cartridge(s). It is then discharged via an (optional) fan set either into the factory or to the atmosphere.
Eventually the dust retained builds up to form a dust cake which effectively improves the collection efficiency of the filter, with a resultant increase in resistance to air flow. To maintain the air flow at the design volume rate, it is necessary to clean this collected dust cake from the surface of the filter media at regular intervals.
Despite the UK having left the EU those who have worked with the ATEX directive and the NFPA standards for combustible dust. Directors should evaluate and classify their working conditions to evaluate the risks. In addition all process and manufacturing equipment should meet the regulations concerning legal and technical standards.
Sangre dust extraction systems meet and exceed the requirements of these various directives when they have been designed, manufactured, installed and commissioned by ourselves.
For more details please do get in touch.
Additional Downloads
A clean working environment helps promote high quality production.
A dust free environment is a great way to keep your premises clean and workers motivated.
Not having dust in the atmosphere improves health by stopping worker breathing in the particles of dust. Healthier lungs make for more productive workers who are more likely carry on working for your company.
Healthier workers are happier and are more likely to remain loyal employees, helping to reduce recruitment and training costs.
Cutting and working with wood is a classic example of a dust problem Sangre are familiar with working with and providing enduring solutions which minimize wood dust very cost effectively. In addition to operator health considerations many machines rely upon being operated in a dust free environment to maintain their accuracy. If there is a build of dust in the working area there is a high chance that accuracy can be affected and compromised. In addition to avoiding spoilt work – the warranty on machines frequently specify that they should be operated in a low dust environment.
Working with machines in a dusty atmosphere can affect bearings and sensors – with our Dustaway extraction system you can extend the working life of machines and the machine sensors.
Why not get in touch today to learn how Sangre can tackle your dust extraction issues.
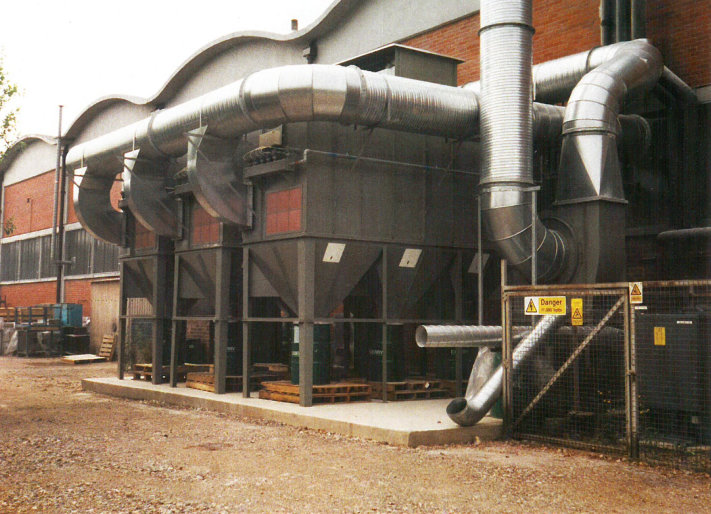
Operational Details
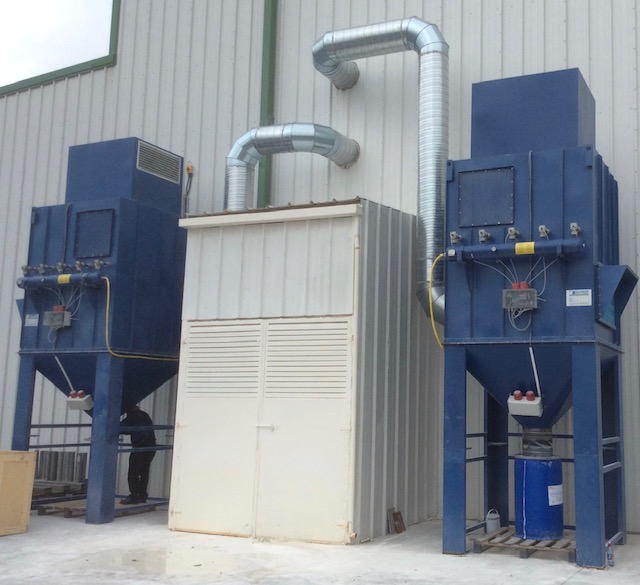
Cleaning is achieved by injecting a short pulse of compressed air into the central internal column of each of the filter elements in turn, against the normal direction of flow of filtered air. This pulse of compressed air momentarily raises the pressure internally to a level greater than the external pressure surrounding the filter element. The higher internal pressure causes a flow through the cartridge in a direction opposite to the normal air flow. This dislodges the accumulated dust cake from the filter media surface.
The effect upon the filtered air flow is virtually negligible, since this method of cleaning a cartridge is achieved instantaneously. Thus the Sangre filter provides for a continuously rated service.
The delivery of compressed air is maintained by a solid state sequence timer activating two way diaphragm valves via solenoids.
A minimal volume of compressed air is required which should be filtered, dry and free from oil, to clean the unit. Air pressure delivered to the unit should be between 5.5 and 6.9 Bar (G).
The dust is collected in a removable bin(s) below the hopper section(s) of the filter. Alternative collecting methods are available for dust discharge, including the use of rotary air seal valve; or indeed a screw conveyer system.
- Roof or floor mounted fans
- Access ladder & platform
- Sound attenuator equipment
- Explosion relief vents and deflectors
- Anti-static & PTFE coating available
- Optional secondary filters
Sangre CF Cartridge Filter Units Capacity Range
- Air volumes between 1000 m3/hr and 25,000 m3/hr
- Units from 5m² to 150m² filtration area.
- Integral fan & motor.
- Various filter media to suit your application.
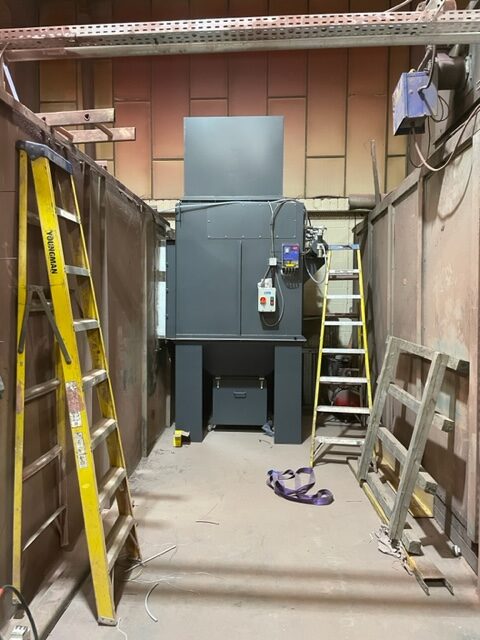
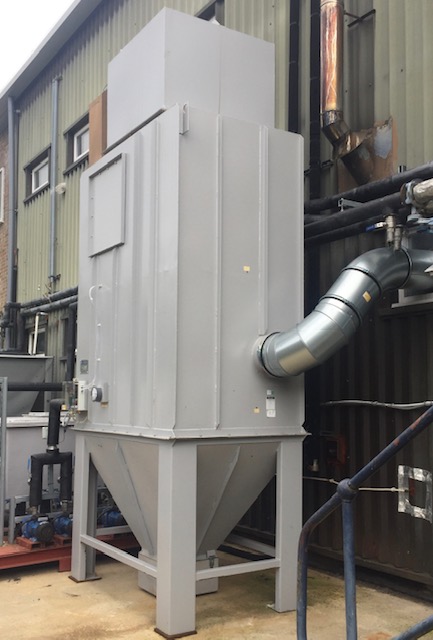
Typical Applications
- Powder Coating booths after filters
- Foundries
- Metal spraying
- Plasma cutting & welding fume (Heavy duty)
- Plastics dust & fume,
- Shot blast
- Food industry
- All Types of finishing Industries
Technical Details
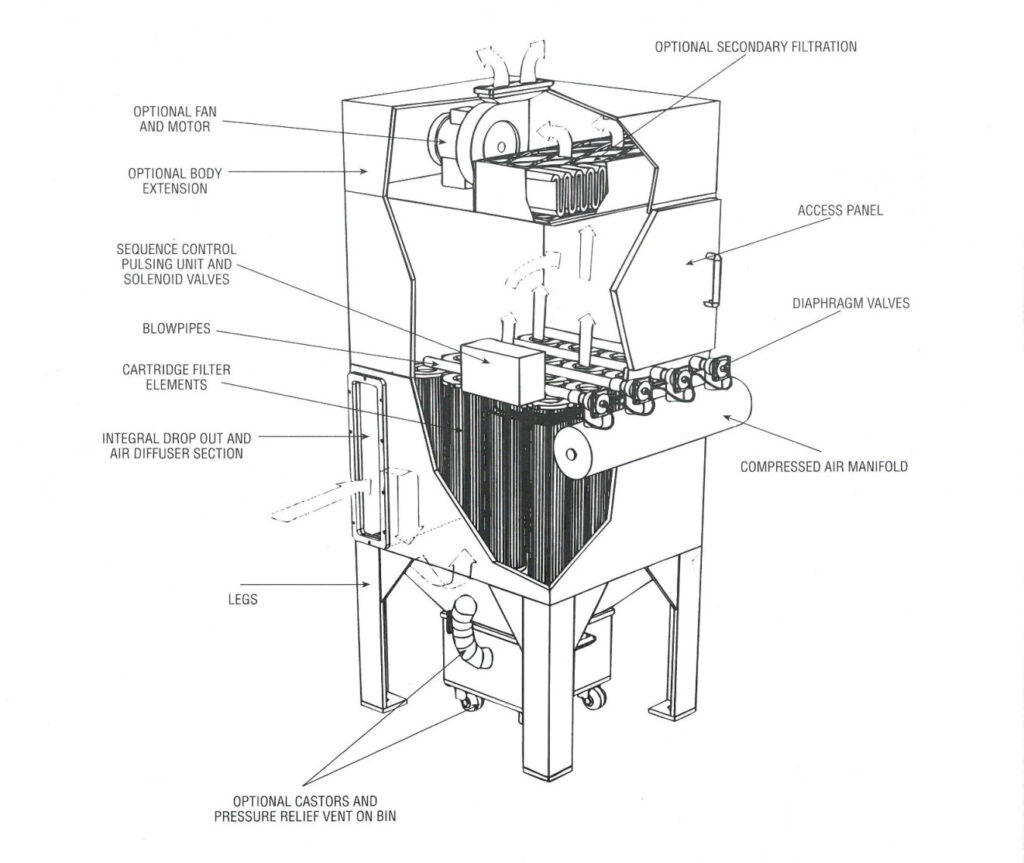
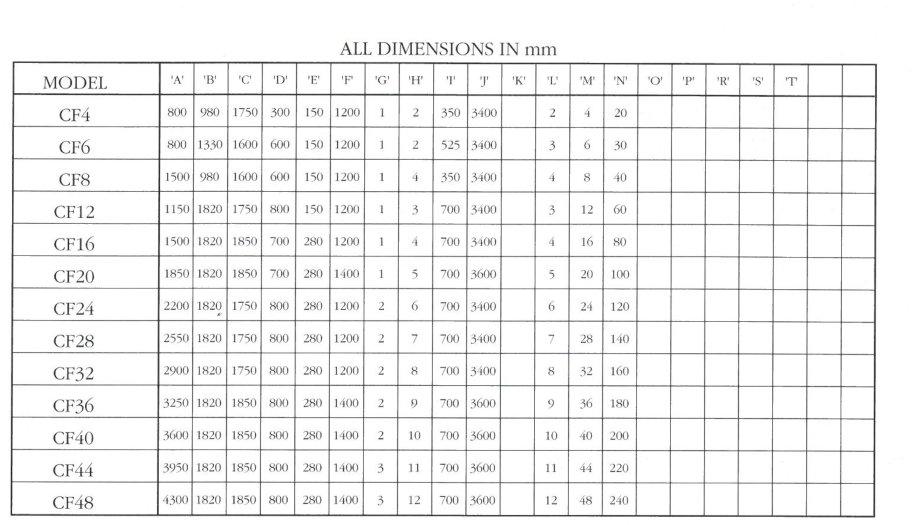
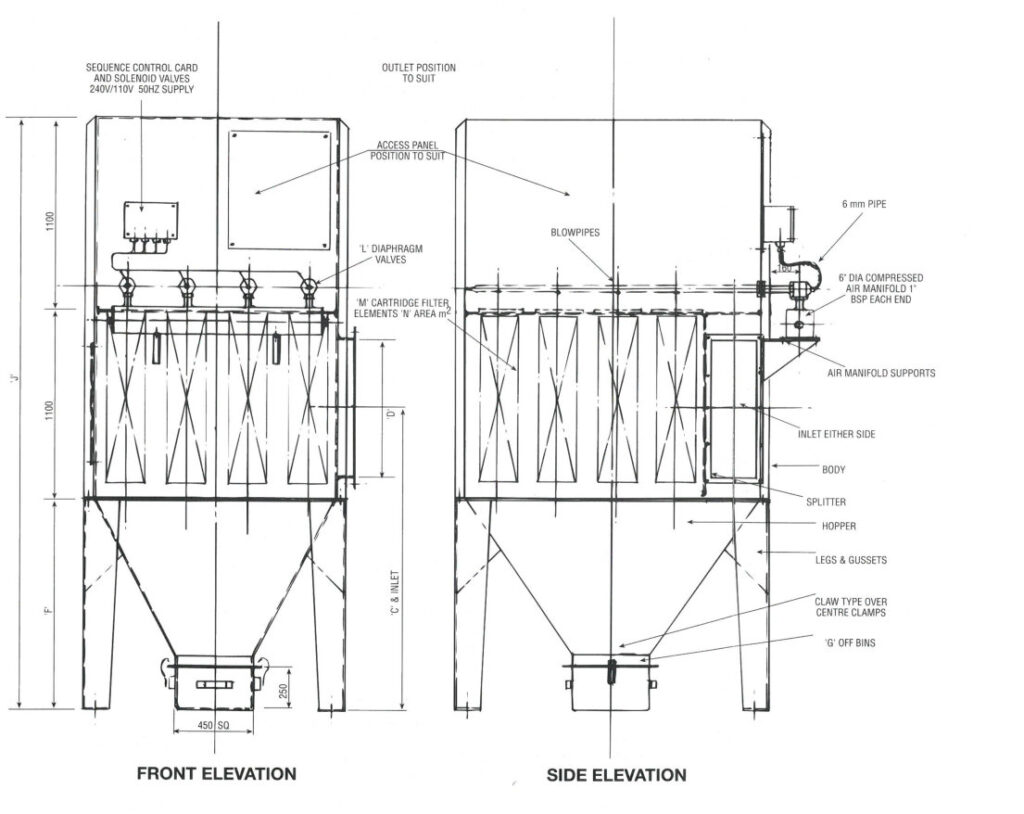
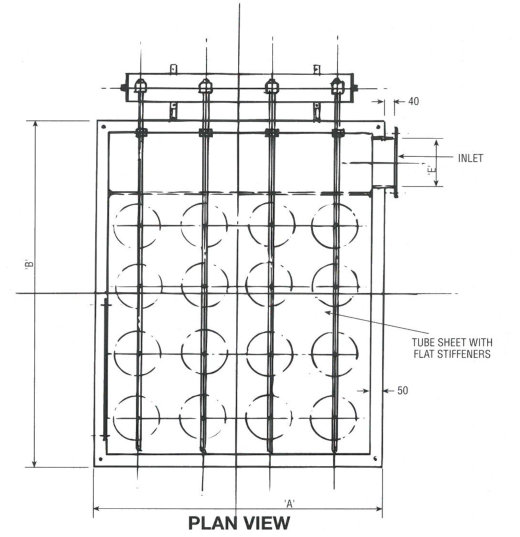
